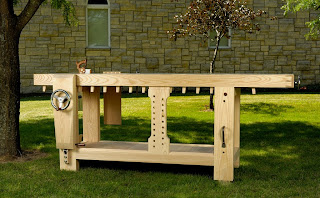
Last year at the
Woodworking In America conference in Valley Forge, PA we received an order for a bench from someone who deserves special mention.
This person is Steve Quehl.
Steve owns the
Woodcraft store in Atlanta, GA. That may not sound like a particularly interesting piece of information, as there are many Woodcraft stores all across the United States. But what makes Steve's store unique is Steve himself. He's a ravenously passionate woodworker, and absolutely dedicated to furthering and elevating the craft. A staunch hand-tool enthusiast, he is equally skilled in bringing fine tools and teachers to the Atlanta area as he is in executing those skills. Steve regularly brings in the heavy-hitters in the modern woodworking community for classes, lectures and demos. Christopher Schwarz, Brian Boggs, Rob Cosman, Kelly Mehler just to name a few. And Steve doesn't stop there. He also regularly attends classes in order to further his own skill (I've seen his work, its absolutely top notch) and to better understand the needs of his clientele at Woodcraft Atlanta.
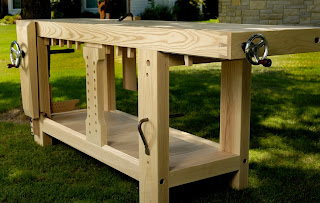
Steve's store is unique in another way. He loves to showcase the best in hand tools from modern manufacturers. He carries planes from Lie-Nielsen and Ron Brese, layout tools from Czeck Edge, Chris Vesper, Glen-Drake and others. Woodcraft Atlanta is also a Benchcrafted dealer. Having such great taste in hand tools, it's no wonder that Steve came to Benchcrafted for a top-notch handcrafted bench. Thanks, Steve for choosing us.
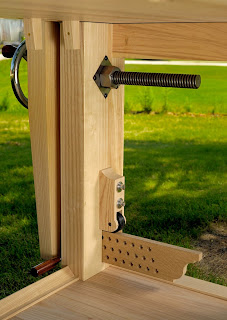
Steve wanted a solid-top Roubo-style bench with massive elements, made of ash. So when we designed this bench we looked back at Roubo's tome and took some cues from the original engraving regarding the base elements. In a
previous entry we discussed the leg dimensions for the bench. We're quite pleased with the result. This bench is rigid as you'd ever need it to be and then some. The bench is 1/4" shy of 8' long, 25" wide and 37" high (Steve is a tall guy). Right now we're not sure exactly how much it weighs, but we're estimating somewhere north of 450 pounds. The bench uses Benchcrafted Barrel Nuts and knocks down into two drawbored end leg assemblies, two long stretchers and the top, which keys onto the legs with four massive tenons. Four Spax lag screws hold the top to the base, although they are not needed, they make it easier to move the bench without the top lifting off the base.
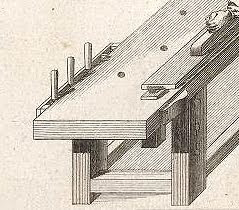
Steve had a couple special requests for the bench. He wanted a tool holder, ala Roubo, placed at the back corner for holding frequently-used tools. We build the holder to remove easily. We drilled and tapped the back edge of the bench for 5/16" flat-head machine screws and applied some gun bluing and light oil to these and all the other fasteners on the bench for a classic look. The tool holder is set 1/4" below the top for clearance.

The outer slot is for storing the planing stop (seen clamped in the leg vise above). We first saw this style planing stop in Chris Schwarz's book on Workbenches and we love it. If you don't have one on your bench, we recommend you make one. It's super simple and really speeds up your work.
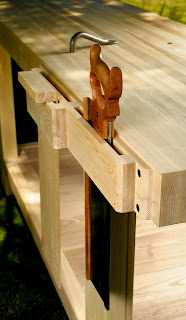
We made Steve's from a wide piece of quartersawn white oak, it's just under 1/4" thin.
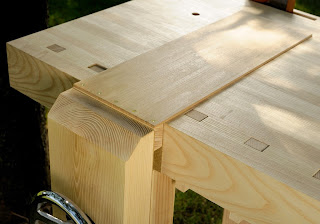
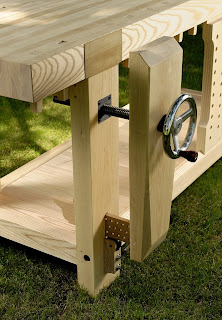
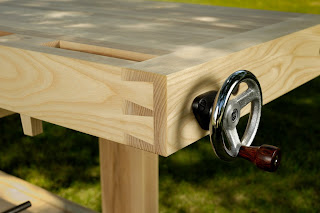
The photos above are while the bench is still "in the white". That's a luthier's term that refers to an unfinished instrument. After all, a bench is an instrument for creating beautiful pieces of furniture.